Pre Engineered Buildings (PEB) Construction: Benefits, Cost & Use Cases Explained
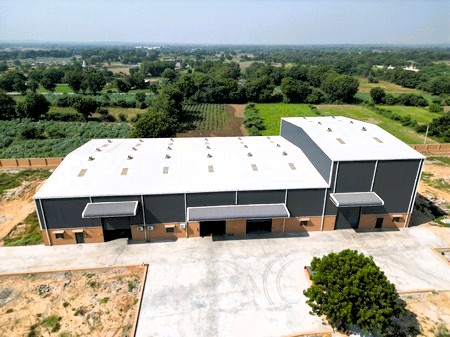
Table of Content
Pre-Engineered Buildings (PEBs) are a modern construction method where building parts, like columns and beams, are made in a factory and then assembled on-site. This method uses standard shapes that fit together easily, allowing engineers to design strong yet cost-effective structures. PEBs are mostly made from steel, making them durable and suitable for various uses, such as warehouses, sports centres, shopping malls, schools, and airports.
One key advantage of PEBs is their quick construction. Since parts are pre-made and delivered ready to assemble, buildings can go up faster and with less waste, which saves money and makes it a more sustainable practice in construction. PEBs are also flexible; if a business or school needs more space later on, it’s easy to expand the building. This makes PEBs a smart choice for places that might grow or change over time
This blog simplifies key concepts and terms in PEBs to help readers understand their unique design, construction, and benefits. For more insights, visit the BuiltX blogs page: BuiltX Blogs
For a detailed overview refer to What are Prefabricated Steel Structures: An Ultimate guide to Pre-Engineered Buildings (PEB)
A. Design Flexibility
- The Primary Framing System: In conventional steel structures, the use of standard-sized hot-rolled sections leads to uniform member dimensions, which can result in over-design in areas where internal stresses are lower. This is because the entire member is sized based on the maximum stress it will experience, leading to excess material in sections that don't require it. In contrast, PEBs utilise a more tailored approach by employing standard plates that can be cut and shaped to align closely with the internal stress distribution, which is shown in below depiction. This allows for tapered members and variable thicknesses in flanges and webs, effectively reducing unnecessary material while maintaining structural integrity. The result is a lighter, more efficient structure that minimises waste and can often reduce costs associated with both materials and transportation. So, By optimising the geometry of each member based on actual stress profiles, PEBs achieve a more efficient use of steel, which can be particularly advantageous in terms of both sustainability and overall project economics.
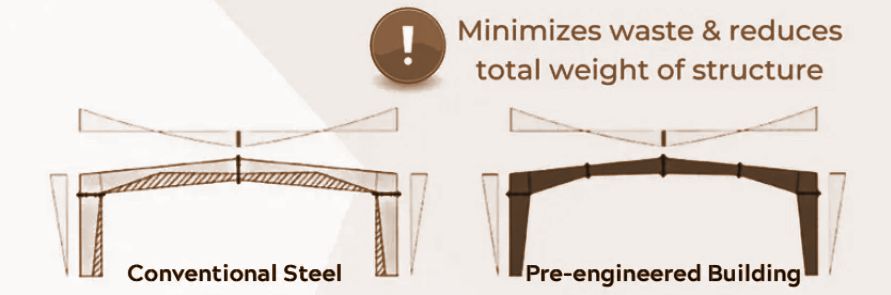
- The Secondary Framing System: These Z-shaped roof purlins and wall girts are used in the secondary framing of buildings and are lighter than the traditional C-shaped sections found in regular steel buildings. When these Z-shaped members are nested (jointed while making an overlap) together at the frames, they work as continuous pieces across the length of the building. This design effectively doubles their strength at the joints, which is where the highest stress usually happens. This helps the structure handle loads better while keeping the overall weight down.
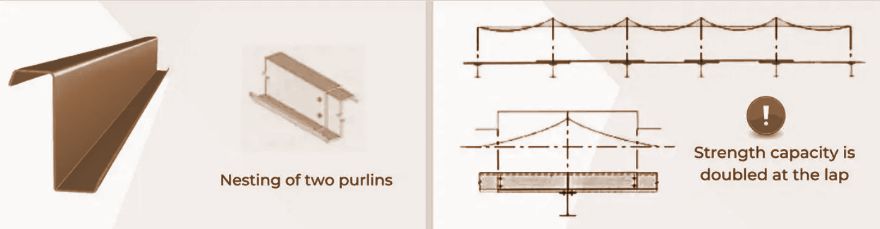
B. Modular Construction:
- In pre-engineered buildings (PEBs), modular technology plays a key role in making construction faster and more efficient. The steel members, like Z-shaped roof purlins and wall girts, are made in a factory under controlled conditions. This leads to a reduction in the time it takes to put things together on-site. These pre-made parts can be delivered directly to the construction site in the order they will be used, which helps keep the project on schedule and reduces clutter at the site. While the steel parts are being fabricated in the factory, the concrete foundations can be built at the same time, further speeding up the entire project. Once the parts arrive, they fit together easily according to the plans, making the assembly quick and efficient. This also means lower costs for putting everything together on-site. Plus, because the steel is made in a factory, it isn’t affected by weather, ensuring high quality and strength. Overall, using modular technology in PEBs leads to faster construction, less waste, and a cleaner work environment.
C. Load Bearing and Structural Stability:
In a Pre-Engineered Building (PEB) structure, the load transfer mechanism works step by step, ensuring the weight from the roof and other elements is safely directed to the ground. Here’s how it happens in simple terms:
- Sheeting Load → Purlins: The outer covering or roof sheeting carries the weight from things like rain, wind, and snow. This weight is first transferred to horizontal beams called purlins, which are attached beneath the sheeting to provide support.
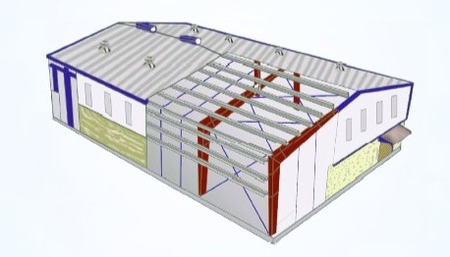
- Purlins Load → Rafters: The purlins don’t carry all the weight on their own. They pass this load down to larger diagonal or slanted beams called rafters, which form the main frame of the roof.
- Rafter Load → Columns: The rafters then transfer this load to vertical supports called columns. These columns run from the foundation up to the rafters and are key to holding up the entire building.
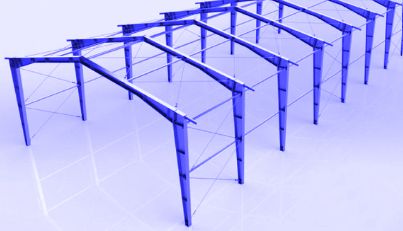
- Columns → Footings: Finally, the columns transfer the entire load down to the footings (or foundations). The footings are built into the ground, and they spread the weight across the soil, keeping the building stable and ensuring it doesn't sink or shift.
In short, the weight of the roof moves from the outer sheeting, down to the purlins, then to the rafters, next to the columns, and finally to the ground through the footings. This systematic process helps keep the structure stable and safe.
The details for different types of PEB buildings are as follows:
- Clear Span: A clear span building is a type of structure designed to have an unobstructed interior space, with no internal columns or supports.

- Single slope: A single slope structure has a roof that slopes in one direction, from one side of the building to the other.
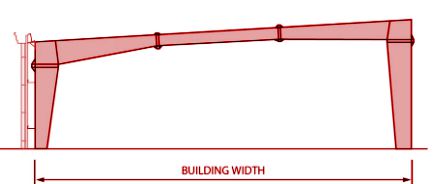
- Multi Span 1: A multi-span 1 building has more than one span, typically supported by internal columns.
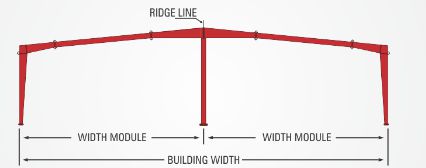
- Multi Span 2: Similar to multi-span 1, multi-span 2 involves more than one span, but with additional interior support columns.
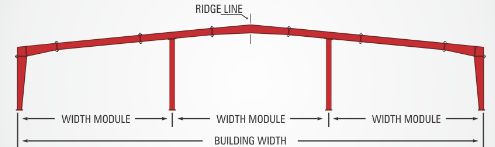
- Multi Span 3: Multi-span 3 refers to a building with three or more spans, each separated by internal columns.
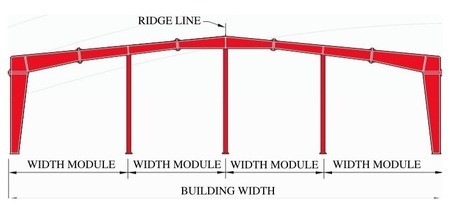
- Multi Gable: A multi gable structure has multiple gable roofs connected side by side.
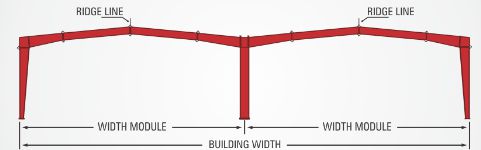
- Lean To: A lean-to is a small building or extension that is attached to the side of a larger structure, usually with a single sloped roof.
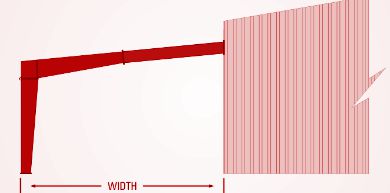
- Built Up Curved Rafter: A built-up curved rafter is a custom-engineered rafter that has a curved profile, giving the roof a distinctive arched appearance.
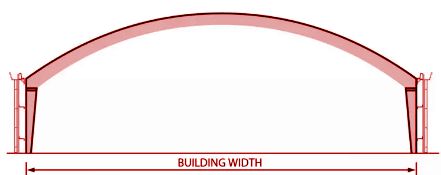
- Roof System: A roof system building has RCC columns instead of PEB columns.
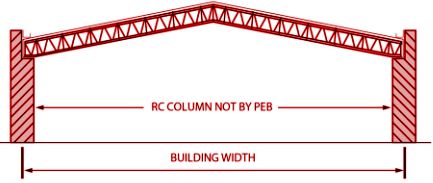
- Clear span with crane: A clear span with crane building has a large open space with no internal columns, but it includes an overhead crane system.
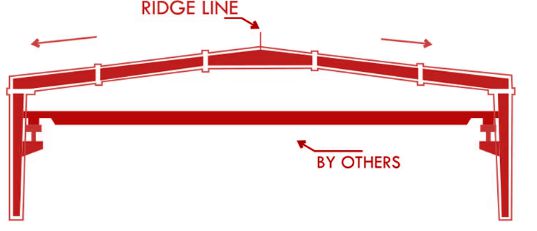
- Multi span with crane & mezzanine: A multi-span with crane and mezzanine is a multi-span building that includes both an overhead crane system and a mezzanine level.
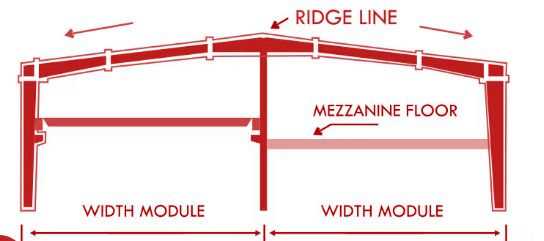
.jpeg)
- Proper use of anchor base plates, either of steel or plywood, for fixing and aligning anchor bolts.
- Plinth beam should be casted in one go, along with use of dowel bars (to make connection with the slab later on).
- If bolting of nuts in anchor requires more time, in the meanwhile brickwork of columns can be completed from 3 sides, outer side being open and backfilling can take place.
- Steel Reinforcement of columns should not exceed the level of bolted nuts.
- Anchor bolt should be properly greased and covered before casting.
- Use of GP2 anchor grout, below base plate in columns.
- Proper use of masking tape should be done in Roof sheeting.
- Shipper List should be matched with the packing list on the site.
Read this article on Rubble Masonry
1. India:
- Bureau of Indian Standards (BIS) guidelines on steel structures (IS 800, IS 801)
- National Building Code (NBC) compliance
- Fire safety approvals from local authorities
- Environmental clearance for large industrial PEBs
2. United States:
- American Institute of Steel Construction (AISC) standards
- International Building Code (IBC) for structural safety
- Energy compliance under ASHRAE
3. Europe:
- Eurocode 3 for steel structures
- CE Marking certification for PEB components
- Energy efficiency compliance under EN 1090
4. Middle East:
- Dubai Municipality’s DM Green Building Regulations
- Saudi Building Code (SBC) for steel construction
Key Insight: PEBs can save up to 30-40% in overall project costs compared to traditional RCC (Reinforced Cement Concrete) buildings.
In conclusion, Pre-Engineered Buildings (PEBs) offer a smart and efficient approach to construction, with their design based on a clear hierarchy of load-bearing elements.
Starting from the sheeting, which faces external forces like rain, wind, and snow, the load is passed through purlins and rafters before reaching the columns and footings, which anchor the entire structure to the ground. This system of load transfer ensures both stability and durability.
Primary components, such as rafters and columns, provide the main support, while secondary components like purlins and girts help reinforce the roof and walls. The outer sheeting protects the building from environmental elements, while ventilation systems ensure a comfortable interior.
PEBs are built using a streamlined process where parts are prefabricated in a factory, reducing both construction time and material waste. PEBs are not only faster and more cost-effective to build compared to traditional methods but are also highly customizable and durable, capable of withstanding various weather conditions. Their eco-friendly design, with reduced material usage and waste, makes them a sustainable choice for modern construction.
Understanding these terms and how PEBs function highlights their advantages in improving design efficiency, speed of construction, and cost savings, making them a practical solution for a wide range of building needs.
Also read, this article about PEBs
1️. What are pre-engineered buildings, and how do they differ from traditional buildings?
Pre-engineered buildings (PEBs) are steel structures where components are fabricated in a factory and assembled on-site. Unlike traditional buildings, which require on-site fabrication, PEBs allow for faster construction, cost savings, and design flexibility.
2️. How does PEB construction improve cost efficiency?
PEBs reduce costs by minimizing material waste, optimizing steel usage, and shortening construction timelines. The pre-fabrication process also reduces labor costs and eliminates weather-related delays.
3️. What are the advantages of prefabricated steel buildings?
Prefabricated steel buildings offer durability, faster construction, sustainability, ease of expansion, and lower maintenance costs. They are also earthquake-resistant and energy-efficient.
4️. How to design a steel building for maximum durability?
A durable steel building should follow structural engineering principles, use corrosion-resistant coatings, comply with local building codes, and incorporate load-bearing efficiency in its design.
5️. What industries benefit most from PEB structures?
Industries such as warehousing, manufacturing, aviation, agriculture, retail, and healthcare benefit from PEB structures due to their quick installation and long-term cost savings.
6️. Are PEBs suitable for earthquake-prone areas?
Yes, PEBs are highly resilient to earthquakes because of their lightweight yet strong steel framework, flexible connections, and ability to absorb seismic shocks without major structural damage.
7️. How do PEBs compare in terms of energy efficiency?
PEBs can be designed with insulated panels, cool roofing, and ventilation systems to reduce heat gain, lowering energy consumption for air conditioning.
8️. What is the typical lifespan of a pre-engineered steel building?
With proper maintenance, a PEB can last 50+ years. Protective coatings and periodic inspections help prevent corrosion and structural wear.
9️. What are the common mistakes to avoid in PEB construction?
Key mistakes include poor site preparation, incorrect foundation design, improper alignment during assembly, and not considering future expansion needs.
10. What permits and approvals are required for constructing a PEB?
Regulatory approvals vary by region but typically include structural safety compliance, fire safety clearances, environmental impact assessments, and local zoning permissions.
Dr. Rajeev Malhotra, Structural Engineer:
"PEB technology is a game-changer in modern construction. The ability to optimize steel usage based on load distribution not only saves costs but also improves structural efficiency."
Amit Verma, CEO of SteelTech PEBs:
"Prefabricated buildings are the future. With rapid urbanization and industrial expansion, PEBs provide a cost-effective, time-saving alternative to conventional brick-and-mortar construction."
ISHA Gupta, Civil Engineer & PEB Consultant:
"The ability to customize PEBs while maintaining high load-bearing strength makes them ideal for industries needing scalable infrastructure."